Vat Photopolymerization
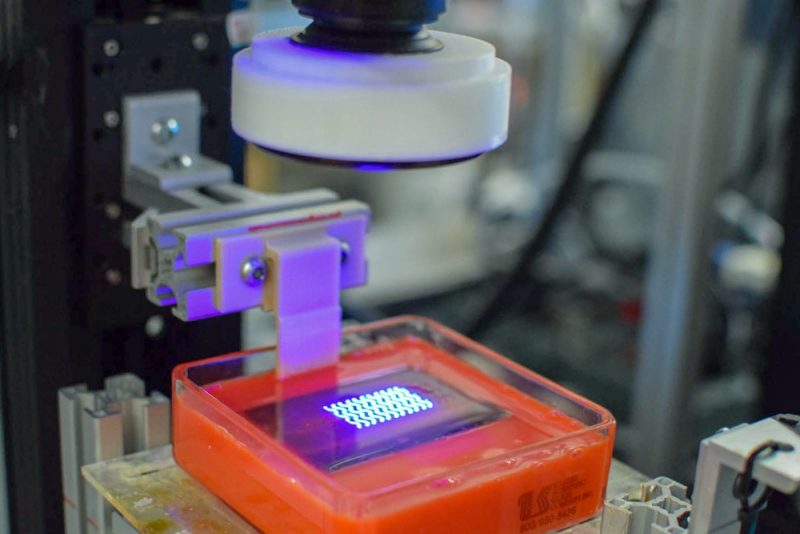
Our Systems
(Custom-built) High-temperature High-viscosity Vat Photopolymerization
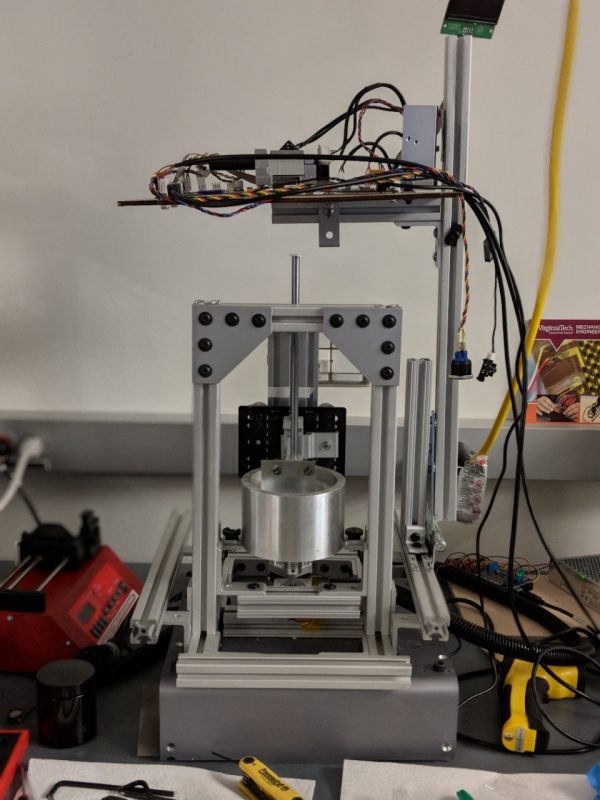
Features and Specifications
- Optimal layer thickness: 150um
- Laser: 64 mW 405 nm laser
- Temperature: 25°C to 200 °C
- Minimum Volume: 150 mL
- Max Viscosity: 100 Pa·s
- Materials: BisGMA-TEGDMA, PEGS-Acetal-Acrylate, BisDMA
Description and Benefits: The high temperature printer is a top-down vat photopolymerization platform that utilizes a 405 nm laser with a max intensity of 30 mW/cm2. The laser rasters across the resin the desired layer shape. With the oven placed atop, the vat is able to reach temperatures up to 200 °C with minimal thermal gradients and the electronic unharmed. The vat is completely aluminum and a metal stage with glass substrate enabling any solvent based resin to be accessible. |
(Custom-built) Scanning Mask Projection Vat Photopolymerization
Features and Specifications:
- Cross-sectional build area of 38.1 mm x 57.15 mm
- Minimum feature size of 300 um
- Optimal layer thickness of 200 um
- Vertical Build Rate of 75mm per hour
- Materials of Objet Veroclear Fullcure 810
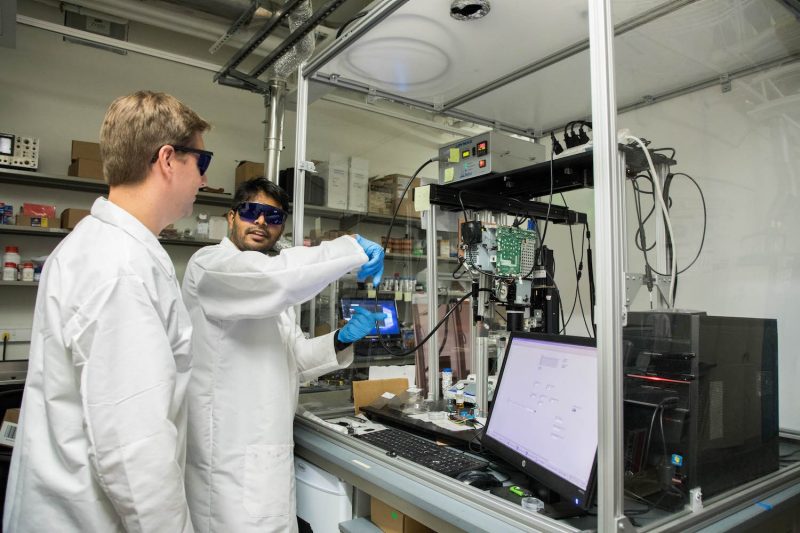
Description and Benefits: This machine uses a broad spectrum light source to cure photopolymers by projecting 2D images using a Digital Micromirror Device. This machine was developed by students in the lab; and unlike commercially available machines, the hardware and operating software of this process can be completely customized for more specialized applications. The constrained surface design cures photopolymer layers between a glass plate and the previous layers. The newest layer is peeled from the glass, which is coated in oxygen inhibiting PTFE Teflon to reduce adhesion. This allows for an economically advantageous process that requires less photopolymer and has a vertical build rate greater than other projection stereolithography systems. The peeling process performed in the constrained surface technique, however, limits the achievable minimum feature size.
(Custom-built) Microscale Mask Projection Vat Photopolymerization
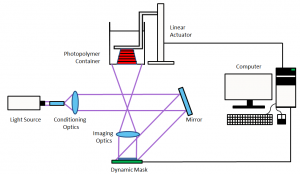
Features and Specifications:
- Cross-sectional build area of 6 mm x 8 mm
- Minimum feature size: 30 µm
- Optimal layer thickness: 25 µm
- Vertical Build Rate: up to 400 layers per hour (material and layer thickness dependent)
- Materials: Poly(propylene glycol) diacrylate (PPGDA), Poly(ethylene glycol) diacrylate (PEGDA), Poly(ethylene glycol) dimethyacrylate (PEGDMA), diacrylate functionalized Pluronic L-31, Pluronic L61, Pluronic L81, Pluronic L-121, Pluronic 10-RS, and many other diacrylate or dimethyacrylate functionalized polymers.
Description and Benefits: MPμSL is an Additive Manufacturing process that uses DLP technology to digitally pattern UV light and selectively cure entire layers of photopolymer resin and fabricate three-dimensional parts. This custom machine uses a UV light source (365 nm) to cure photopolymers layer by layer. As opposed to Constrained Surface Stereolithography machines, this machine projects from the top which results in somewhat higher resolution on the order of tens of microns. MPµSL is an excellent solution for building small parts with extremely high resolution and thus this technology is well suited for fabricating tissue scaffolds. This machine is also being used to characterize novel polymers that are being synthesized in a collaboration with Timothy Long's lab in the Department of Chemistry.
(Custom-built) High-temperature Vat Photopolymerization
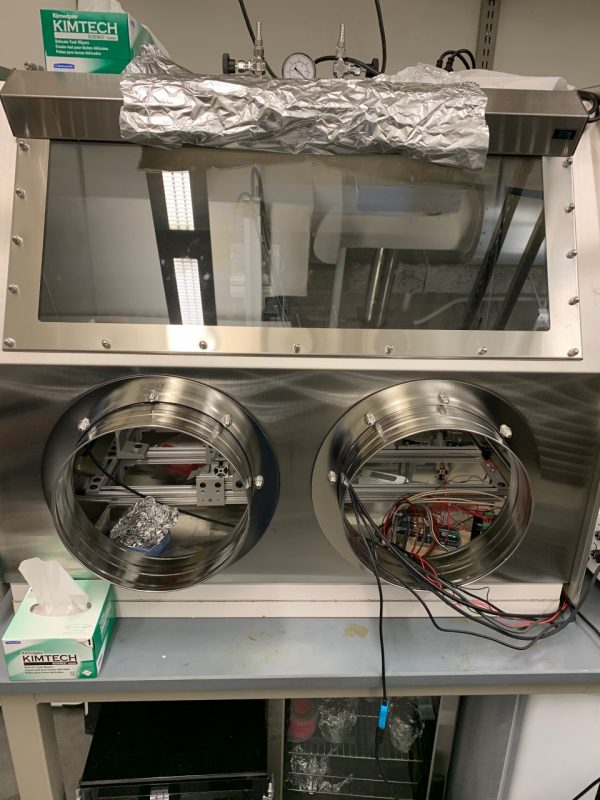
Features and Specifications:
- Optimal layer thickness: 150 µm
- Source: 30 mW/cm2 405 nm LED mask projection
- Materials: High viscosity resins, solvent based resins
- Temperature: 25 °C to 200 °C
- Minimum Volume: 150 mL
Description and Benefits: The high temperature printer is a top-down vat photopolymerization platform that utilizes a 405 nm LED with a max intensity of 30 mW/cm2 which goes through a mask to get patterned. With IR lamps, the vat is able to reach temperatures up to 200 °C with minimal thermal gradients. The vat is completely metal and a metal stage with glass substrate enabling any solvent based resin to be accessible. |
FormLabs Form 1+
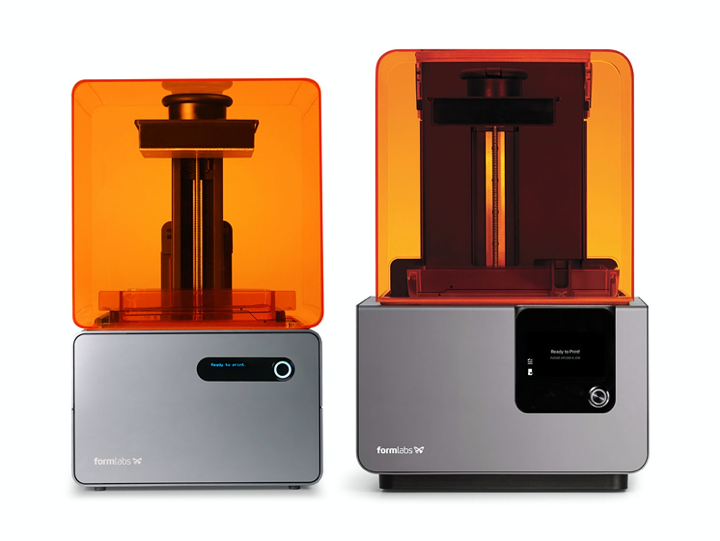
Features and Specifications:
- Cross-sectional build area of 125 mm x 125 mm
- Minimum feature size: 300 µm
- Optimal layer thickness: 25 µm
- Vertical Build Rate: material and layer thickness dependent
- Laser: 64 mW 405 nm laser
- Materials: FormLabs resins (Clear, Black, Castable, Flexible, Tough, etc)
Description and Benefits: The FormLabs Form 1+ is a bottom-up vat photopolymerization platform that uses a rastering laser to scan the shape and infill of the layer. The Form 1+ is not open sourced thus material selection is limited to FormLabs’ products. This printer uses a 64 mW, 405 nm laser and maximum scan speed of 2500 mm/s. This printer uses a transparent window and a large bulid area resulting in large peel force for large area layers. This printer is being used to generate sacrificial molds for casting metals. |
Autodesk Ember
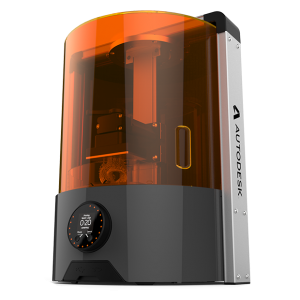
Features and Specifications:
- Cross-sectional build area of 64 mm x 40 mm
- Minimum feature size: 150 µm
- Optimal layer thickness: 25 µm
- Vertical Build Rate: up to 18 mm per hour (material and layer thickness dependent)
- Materials: Poly(ethylene glycol) diacrylate (PEGDA), Poly(ethylene glycol) dimethyacrylate (PEGDMA), other diacrylate or dimethyacrylate functionalized polymers and ceramic suspensions.
Description and Benefits: The Autodesk Ember is a bottom-up MPμSL system that uses DLP technology to digitally pattern UV light and selectively cure entire layers of photopolymer resin and fabricate three-dimensional parts. This commercialized machine is open sourced which enables the user to control printing parameters, customize its firmware, and print from third-party resins. This printer uses a UV light source (405 nm) that is digitally patterned from an array of mirrors spaced 7.6 microns apart on the digital micromirror device to selectively cure photopolymers layer by layer at the micron scale. This machine projects from the bottom which enables a larger build volume but at a small expense of resolution compared to top-down MPμSL systems. The design of the Autodesk Ember is also completely open source, with CAD files of each component available online to encourage machine modification and its electronic components for exploring print constraints. This machine is currently being used to fabricate ceramic structures in our lab and novel polymers synthesized in a collaboration with Timothy Long‘s lab in the Department of Chemistry.
Active Projects
-
General Item
Past Projects
-
General Item
-
General Item