Hybrid Wire Arc Additive Manufacturing
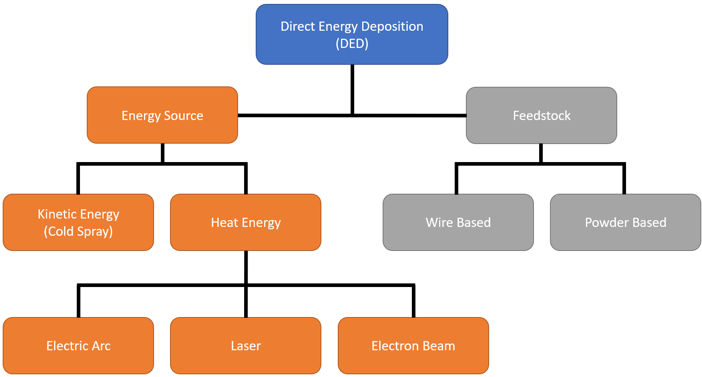
Directed Energy Deposition Overview
Hybrid Wire Arc AM is a subcategory of Directed Energy Deposition (DED), an additive manufacturing technology that is implemented to process a wide range of metallic materials using a 1D heat source to melt and deposit material layer by layer. This process is carried out by simultaneously feeding material and applying a concentrated energy source using some sort of robotic arm. The build volume is only limited by the reach of the robotic arm or the material selected for processing. Certain metallic materials can be processed in an open environment either by applying a shielding gas during material deposition or by using flux core material making reach of the robot arm the major the build volume limitation. There are metallic materials that require inert environments for processing which can limit the build volume.
DED can be divided into two groups, the type of energy source and the type of feedstock material. There are two types of energy sources, one being heat energy and the other being kinetic energy (cold spray). The applied 1D heat source can come in a variety of forms including laser beam, electron beam, and electric arc. There are two types of feedstock, one being powder based and the other wire based.
Our Systems
DMS 2Cubed Hybrid Metal Additive System (H-6222A/S)
The DMS 2Cubed system is capable of building parts up to 2'x2'x2' in a variety of ferrous and non-ferrous metal alloys via a hybrid Wire-Arc AM (hWAAM) process where a short circuit Gas Metal Arc Welding (GMAW) process is paired with a traditional 3-Axis CNC machining center. The system can deposit more than 5lb of material per hour, and is capable of precise features by finish machining the near-net-shape printed part. hWAAM systems are in general capable of building much larger components than other metal additive manufacturing processes, and have substantially lower material costs, facility footprints, and complexity. For this reason, hWAAM is an attractive process for any large metal component where production quantities are low, and especially in remote environments. The system is being used to conduct research into material performance, control system optimization, and process aware path planning in partnership with the Naval Surface Warfare Center, Carderock Division (NSWCCD). The system is on long-term loan to the DREAMS lab through our Cooperative Research and Development Agreement with NSWCCD's Additive Manufacturing Branch.
Active Projects
-
General Item