Fabricating Bioceramic Parts Using Vat Photopolymerization
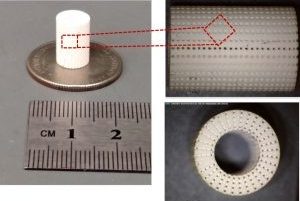
Project Overview
Goal: Fabricate functional ceramic parts from a photocurable suspension using vat photopolymerization.
Description: Ceramics are chemically inert, heat-resistant, lightweight, and high-strength materials due to its packed crystalline structure comprised of strong ionic or covalent bonding between metallic and non-metallic atoms. Additive manufacturing of ceramics provides design freedom to selectively place ceramic material into three-dimensional space to leverage their intriguing material properties. In our research, we integrate micron to nano-sized ceramic particles such as calcium phosphate and aluminum oxide at high loading concentrations into photocurable polymer and organic dispersant to create a resin with viscosities suitable for vat photopolymerization. VP is used to selectively cure photopolymer using ultraviolet light to bind ceramic particles layer by layer to form a three-dimensional green body that is later consolidated into a densified ceramic after thermal treatment and sintering.
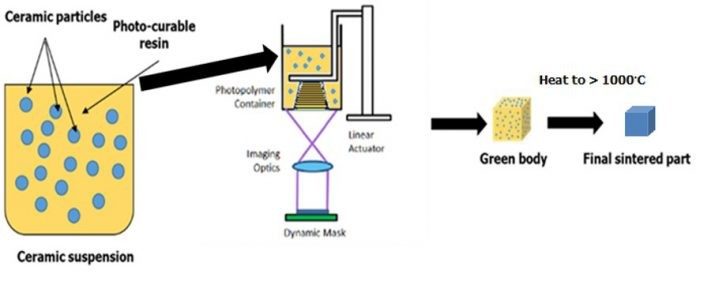
Literature suggests loading ceramics above a concentration 50% by weight is necessary to print a green body using stereolithography that can be sintered into a ceramic part with high density. (Halloran et al., 1997) Other considerations in forming the suspension suitable for printing must be taken into account such as minimizing the refractive index difference between the ceramic particle and the photocurable polymer resin. Also, the dispersant plays a role in maintaining a low viscosity in the overall ceramic suspension to allow recoat in between layers.
Ceramic parts fabricated in our lab retain micro-scaled features after sintering while maintaining structural integrity and sufficient strength. We envision the combination of ceramic properties, suspension formulation development, and engineering design to build reliable, wear-resistant, high-resolution 3D structures used in electronics, thermal insulators, medical implants, automotive parts, water filtration among others.
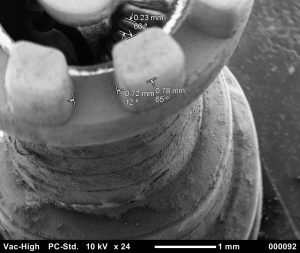
Research Lead
Donald Aduba Jr.
Sponsors
Industrially Sponsored