Manufacturing Considerations for Multi-Material Compliant Mechanisms
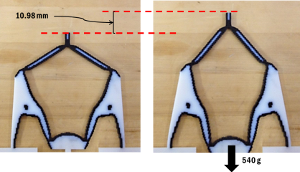
This project is, in part, motivated by the idea of creating optimized, actuating structures using modern Additive Manufacturing (AM) processes. Specifically, there are three distinct categories of research that all contribute to this overall motivating idea: 1) development of a multi-material topology optimization process for multi-material jetting, 2) understanding the role that manufacturing constraints play in the fabrication of optimized structures, and 3) development of a process for embedding actuating elements within material jetted parts. The scope of this work focuses mainly on the latter two of these realms with an emphasis on the PolyJet Material Jetting subset of Additive Manufacturing processes, which is the only commercially-available process capable of creating multiple-material compliant mechanisms with embedded components to support actuation. Research questions focus around considerations of minimum feature size, material anisotropy, and support material removal, in addition to the role of multi-material limitations, which might cause the as-manufactured part properties to differ from the optimal design.
Research Lead
Nick Meisel