Post-Consumer Waste Stream Plastics as a Source for Material Extrusion Additive Manufacturing
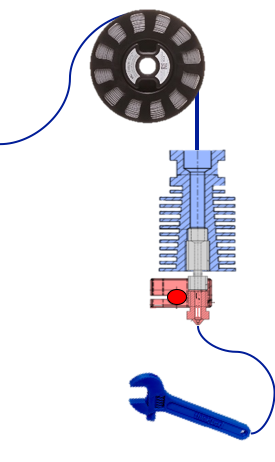
Project Description:
Material extrusion additive manufacturing (AM), also known as Fused Deposition Modeling™ 3D printing, is the most prevalent of the seven AM technologies. Although extrusion AM allows for greater design freedom than traditional forms of manufacturing, the currently low variety of polymeric materials suitable for this process greatly limits the applications of extrusion AM. The proposed work adapts the decades of research in polymer blending for injection molding and other traditional manufacturing methods to the fabrication of filament for extrusion AM. Two component polymer blends offer the ability to tune thermomechanical properties through different blend ratios; however, polymer blends are often not compatible for all component ratios. Through this work, I will determine blending ratios for three two-component polymer systems, one three-component polymer system, and one system involving recycled and neat versions of the same polymer suitable for 3D printing. The candidate polymers are chosen for their presence in industrial waste streams so that this work will pave the way for a cradle-to-cradle lifecycle for these blends as waste streams are recycled into 3D printing filament. These blends enable a greater variety of products to be made via AM and an additional avenue for recycling post-consumer and post-industrial plastics.
Project History:
Since its inception in the 1980’s, additive manufacturing (AM), commonly known as 3D printing, has been hailed as a “manufacturing revolution” allowing designers the freedom to create complex geometries not previously achievable by traditional, subtractive manufacturing methods. AM is also revolutionizing the manufacturing supply chain by supporting the “just in time” or “print on demand” paradigm enabling companies to carry less inventory on hand. In addition, AM has a reputation for being “greener” than traditional, subtractive manufacturing techniques as it only deposits material where needed, thereby generating far less material waste.
This proposal focuses on material extrusion AM, also known as Fused Deposition Modeling™ (FDM) and depicted by the cartoon in Figure 1. It is a melt-based process using thermoplastic polymers to build an object layer by layer from a digital computer aided design (CAD) file. Extrusion AM is the most common type of AM technology in terms of units sold which is why it was selected for this proposal.7
AM may be an inherently less wasteful process than injection molding, but we want to go beyond reducing waste towards reversing the negative effect on the environment by capturing post-consumer water bottle waste and post-industrial manufacturing line waste as sources for feedstock. Consumer water bottles are made from poly(ethylene terephthalate) (PET, recycling code #1) thermoplastic, which is the type of polymer needed for extrusion AM. Other thermoplastic polymers commonly found in industrial waste streams include polyamide 6,6 (nylon), polypropylene (PP, recycle code #5), and polyethylene (PE, recycle codes #2 and #4).
Although less wasteful, AM suffers from a severely limited selection of materials in comparison to traditional manufacturing methods, such as injection molding. Recently, the AM community has identified the lack of materials suitable for AM as an area of critical need for research.2,3 The materials used for processes like injection molding are not “plug and play” as AM imposes unique constraints on material selection, such as the need to quickly melt and quickly solidify to maintain the shape of the part without an external support such as provided by the molding process. Therefore, our proposed research addresses this high-needs area by exploring how to adapt decades of polymer blending research to enhance the sustainability and materials catalog for this transformative technology.
Prior Work .
Polymer systems composed of multiple polymers types tend to macro-phase separate, which often results in thermomechanical properties worse than either of the original single component systems. Researchers have determined specific compatibilization methods for certain polymer pairs enabling synergistic blending to achieve properties better than if the blends followed the rule of simple mixtures. Successful compatibilization of the following multi-component blends have been achieved for traditional manufacturing methods, such as injection molding and film extrusion: polyethylene and polyamide 6,6 and poly(ethylene terephthalate) and polypropylene.
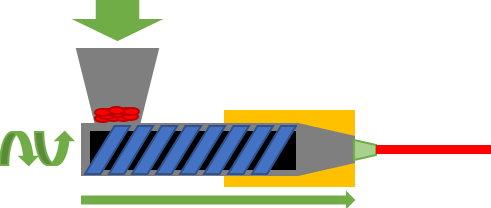
Broader Impact
The proposed work centers on enhancing the sustainability of AM through demonstrating the process needed for transforming trash into raw material. As AM is increasingly used as means of introducing K-12 students to design and engineering, this will empower schools to train the designers of tomorrow while minimizing their environmental impact. In addition, this advances the growing field of AM through expanding the catalog of materials identified as suitable choices. This expansion opens new opportunities for designers to take advantage of the geometric complexity, single tool manufacturing, and sustainability offered by AM while also having their desired material properties in the final product. This research paves the way for several new systems of polymer blends to be redirected from landfills back into the supply chain thus enabling water bottles and other products to find a new life as prototype models, custom tooling, and 3D printed trinkets.
Related Presentations
G. Godshall, C. A. Chatham, C. B. Williams. “THERMAL AND MORPHOLOGICAL CHARACTERIZATION OF VIRGIN AND RECYCLED PET/PP BLENDS FOR MATERIAL EXTRUSION ADDITIVE MANUFACTURING” MII Technical Conference and Review. April 15, 2018. Blacksburg, VA
Research Lead
Garrett Godshall, Camden A. Chatham